Ibstock Concrete is to invest across its extensive UK manufacturing facilities to improve the safety and efficiency of its operations by undertaking innovative upgrades to its engineering practices.
Following extensive employee feedback, Ibstock Concrete has made significant upgrades to the manufacturing processes at its Bedford and Northwich sites, which manufacture a comprehensive portfolio of landscaping, flooring, building, rail and infrastructure products for its industry leading Supreme Concrete and Anderton Concrete brands.
At its Northwich facility, Ibstock Concrete has achieved a unique and industry leading approach to the casting process, which consistently reduces the trigger time for vibration to below the HSE’s Control for Vibration at Work Regulations 2005 Daily Exposure Limit Value.
Following an in depth review of the existing casting process, which involved filling moulds with concrete and applying vibration at 55Hz to remove any air voids, a three stage visual indicator and three level vibration system has been installed.
This process is not only a new concept for Ibstock Concrete, but is a revolutionary approach for the entire industry, as it effectively reduces the associated risks of high levels of potential exposure to vibration, by providing individuals with real time information on the level of vibration the manufacturing equipment is currently operating at.
Even on the highest setting, a vibration survey has evidenced the potential exposure limit as low as 2.7 m/s2 A(8), whilst on the lowest setting, the potential exposure is as low as low as 0.5m/s2 A(8), both of which are below the HSE's Daily Action Limits.
Following the success of this new process and its reflection of best practice, a plan is in place to phase in the technology across all Supreme Concrete and Anderton Concrete manufacturing sites where vibrating tables operate.
As part of this dedicated programme of investment, Ibstock Concrete has also reviewed its slotted post casting process at its Bedford facility. Following extensive employee consultation, reducing the frequency of manual handling required was identified as a key priority, to ensure the consistent safety of all operatives, without affecting the overall manufacturing process.
As a result, a central element of the production process has been automated through the installation of a dedicated rebate lifter, which mechanically lift the rebate from the cast product.
This eliminates the operator having to physically lift the rebates from the mould, substantially reducing the level of manual handling required by the operator.
The automation of this process is a completely new approach, again not only for Ibstock Concrete, but for the entire industry, as it modernises a traditional and established stage of the casting phase.
This technology is now being implemented across all relevant Ibstock Concrete manufacturing sites throughout the UK, providing an even safer working environment for employees by considerably reducing manual handling with the aid of mechanical means and in accordance with the HSE’s Manual Handling Operations Regulations.
Construction News
05/10/2021
Ibstock Concrete To Upgrade Its Engineering Practices
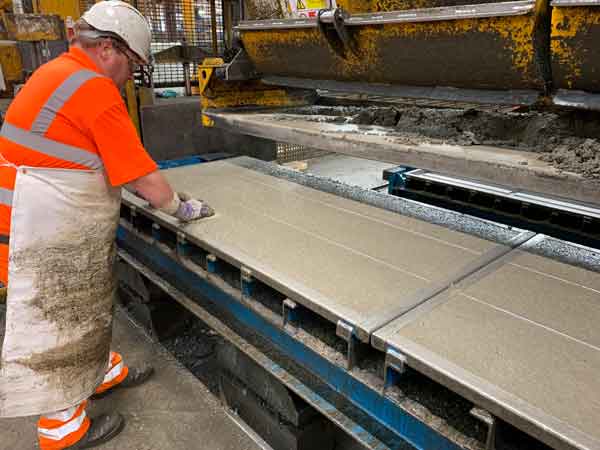
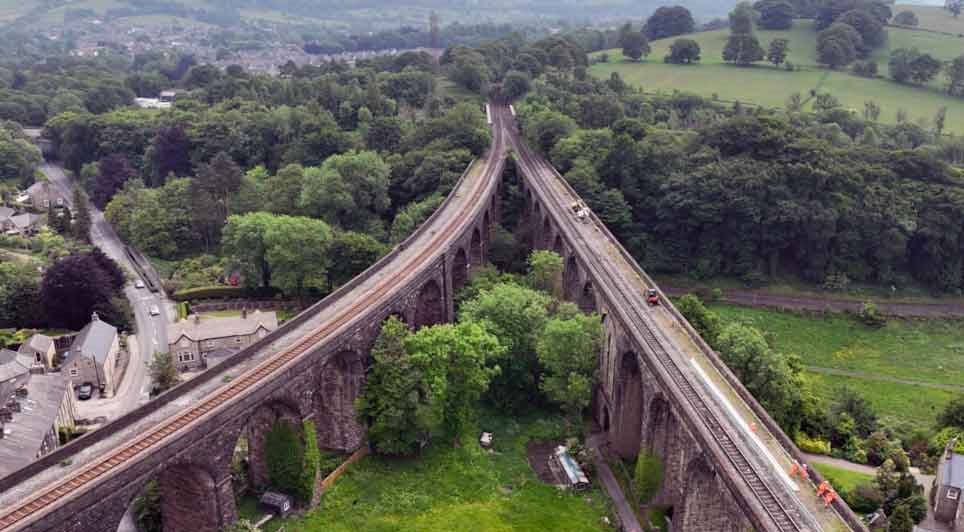
13/06/2025
A vital piece of Peak District railway infrastructure is set to receive a major upgrade this summer, as Network Rail announces a £7.5 million investment into one of Chapel Milton's iconic twin Victorian viaducts.
The 160-year-old, 15-arch structure plays a critical role in the UK's freight network,
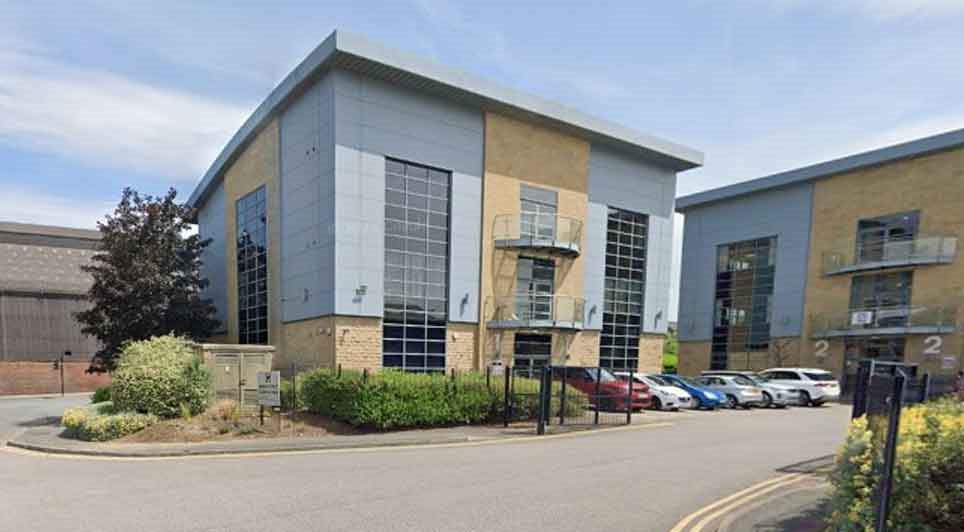
13/06/2025
Morgan Sindall Construction has revealed plans to expand its operations in South Yorkshire, building on its strong delivery record in West Yorkshire and aligning with the goals of the newly launched Great North initiative.
Backed by northern regional mayors, the Great North initiative aims to unloc
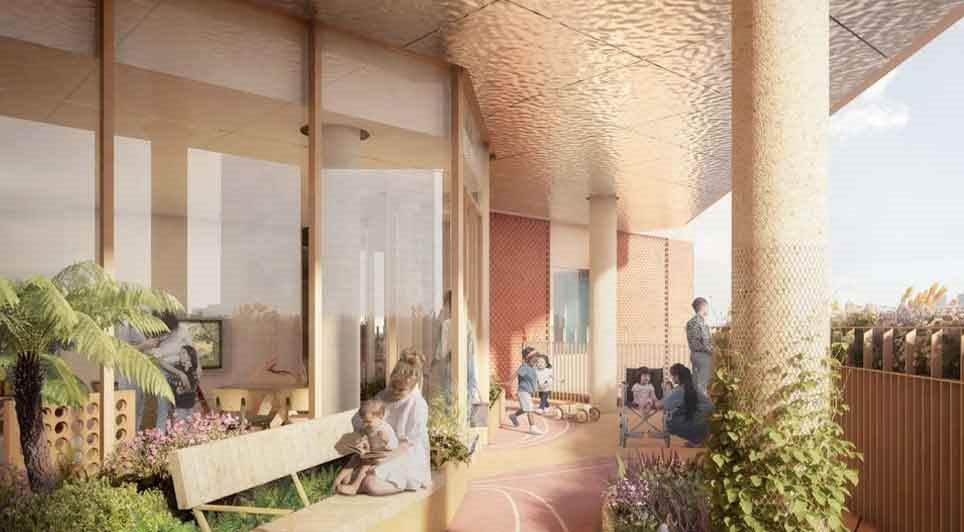
13/06/2025
Construction has officially commenced on the new Children's Cancer Centre (CCC) at Great Ormond Street Hospital for Children (GOSH).
Led by long-term design partner BDP, the new centre is one of the most ambitious projects in GOSH's history. The firm is overseeing architecture, landscape, engineeri
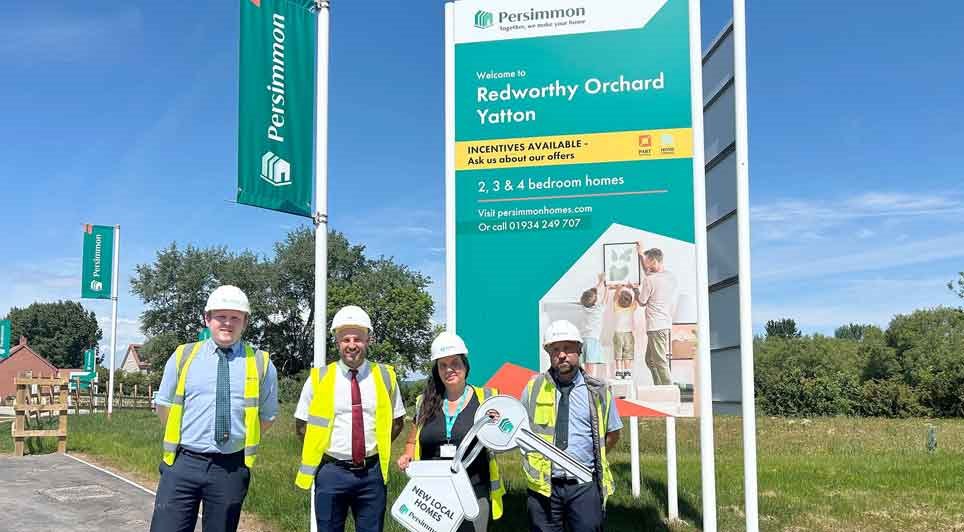
13/06/2025
The developer behind the Redworthy Orchard scheme in Yatton has handed over the first homes to a local housing association as part of a wider plan to provide affordable housing in the area.
Persimmon Homes Severn Valley has transferred four new properties to Alliance Homes, a move set to ease press
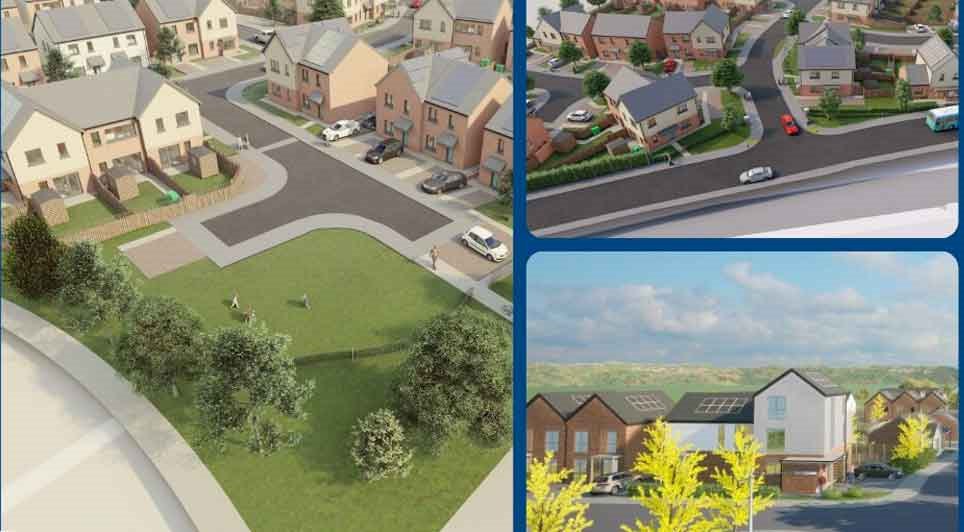
13/06/2025
Wynne Construction has been awarded two major design and build contracts worth over £20 million by Adra to deliver nearly 100 new social homes across North Wales.
Construction is already underway at the first site on Berse Road, Wrexham, where Wynne began work in March on a £9 million, 47-home soci

13/06/2025
Great Places Housing Group has officially broken ground on its landmark £37 million LGBTQ+ majority Extra Care housing scheme in Whalley Range, marking the start of construction during Pride Month.
The scheme, hailed as the UK's first purpose-built Extra Care development of its kind, is being deliv
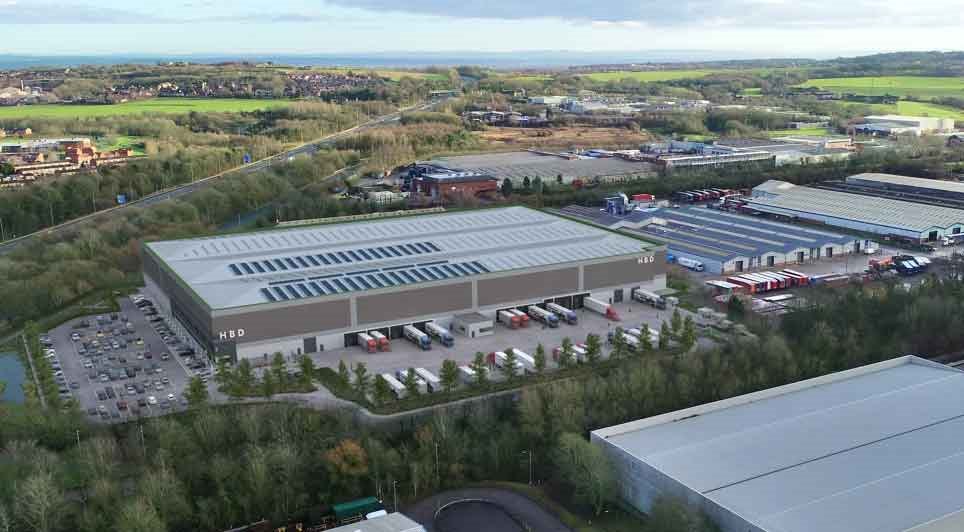
13/06/2025
Henry Boot PLC has announced that its property investment and development arm, HBD, has completed the sale of TWO45, a multi-let industrial-led business park in Skelmersdale, to a European real estate developer for £9.5 million.
Located on a 10-acre site just minutes from the M58 and M6 motorways,
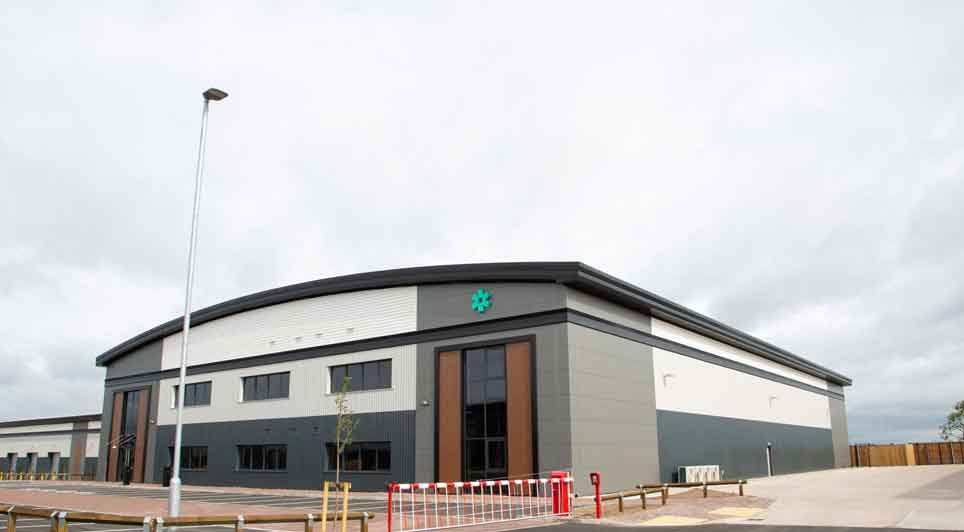
13/06/2025
Clowes Developments has announced the successful letting of Unit 5A, a newly completed 27,000 sq ft industrial unit at Stud Brook Business Park, to Shawpak Ltd, a pioneering manufacturer of medical device packaging machinery.
Founded in Derby in 2013, Shawpak Ltd designs and produces a unique range
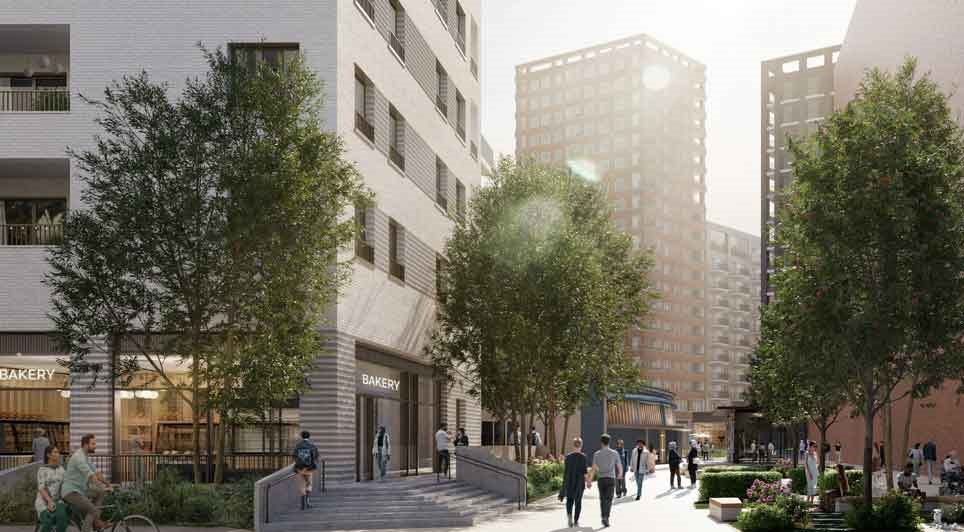
13/06/2025
The Hill Group and Legal & General (L&G) have announced a new partnership to deliver 200 affordable homes as part of the first phase of the £450 million City Centre South regeneration scheme in Coventry.
This marks the first time the two organisations have collaborated on a major residential devel
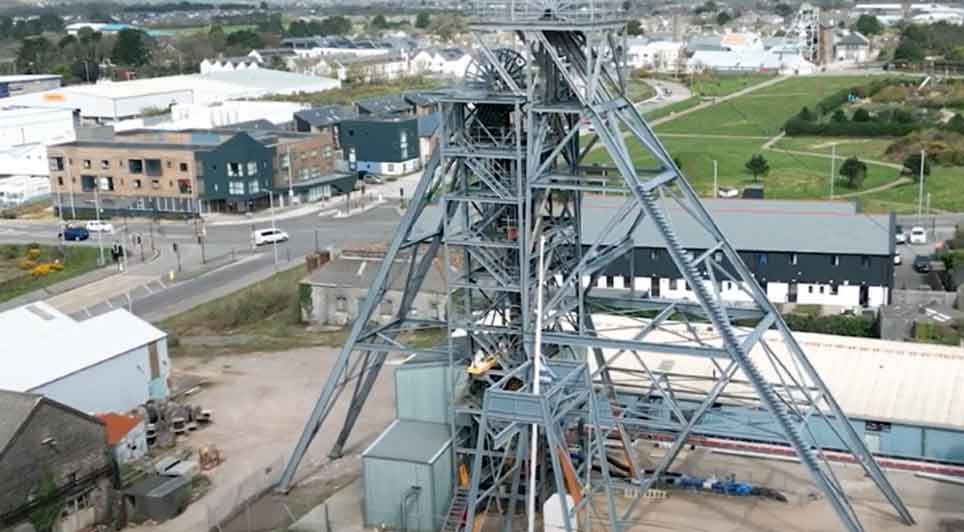
13/06/2025
The historic South Crofty tin mining project in Pool, Cornwall, is set to receive a significant boost after being awarded £4,190,500 through the Cornwall and Isles of Scilly Good Growth Programme, marking the largest single private sector investment by the programme to date.
Delivered by Cornwall C